When you bring new farm workers in to your workplace, you may get frustrated watching them do things the wrong way. Perhaps they do something you see as silly or not using ‘common sense’.
Assuming people know how to do the job properly is a gamble which could cost a lot if something goes wrong in farming. Broken machinery, broken infrastructure, broken people. All are costly mistakes, and generally easily avoidable.
By giving new farm workers some basic training and instruction, you set them up to succeed. After all, that’s why they’re here. How and what to do for this is easy.
How to get started
Start with an induction on their first day. This should talk about the business, property layout and expectations of their employment.
Be sure to include basic information about the following:
- Where things are
- Start and finish times
- Meal breaks
- How much and when they get paid
- What they need to do for timesheets or to apply for leave
- And, who to go to with any additional questions
Safety Information
Now you have covered the basics that most new employees want to know, now it's time to talk about the things they have to know, to keep them safe.
This includes:
- Company policies
- Consultation processes
- Emergency information (first aid, fire, medical emergency etc.)
- Correct use of equipment and PPE
- Where known hazards are
- And, how to report an incident or new hazard
Now let's take a look at the job at hand
Once you have the company basics covered and invested some time going through general safety information, then look at tasks – how do you know if they know how to do the job at hand?
It’s a smart investment of time to check to see if they are competent, or whether they may need some training or instruction.
The safest option is to go through things with all new workers, even if they are an experienced hand. Every property has a different way of doing things or different expectations, so make the time to take new workers through how things are done.
Training and instruction
Training and instruction don’t necessarily need to be anything formal, although this can be a good option in some cases. For example, if you have a forklift that workers use, you must ensure they have the appropriate licence from a Registered Training Organisation. Just being able to use a forklift isn’t enough.
However, for something like a tractor there’s no formal qualifications needed but it’s just as important to make sure operators are competent. That’s an expensive piece of machinery in their hands, which can do a lot of damage if not operated properly. That’s where on the job instruction is beneficial.
Whatever method/s used to verify a worker is competent, make sure you keep a record of this. That might be getting a copy of their licence/ticket or qualifications, or by taking them through an on-the-job induction for a task or use of machinery and getting this signed off.
Don't forget to keep up with ongoing training
Even workers that have been with you for a while need training too. New equipment, new processes and even new chemicals need some kind of upskilling to ensure safe use and operation. Again, this can be formal or informal and good record keeping is advised.
Experienced hands might want to learn new skills too. Investing in developing your workforce is smart as you’ll have a more efficient operation with less likelihood of serious incidents.
Some of the formal training needed in many agricultural businesses include:
- Forklift
- Confined Spaces
- Working at Heights
- Safe use and handling of chemicals
- First Aid
It can be a useful exercise to create a training register.
Find out how Safe Ag Systems registers and keeps track of employee training.
Write down the different role and tasks on your property, and think about what licences, training and/or competency a worker needs to do the job safely. Then you’ve got a guide as to what workers need.
For example, spraying will mean a worker needs Safe use and handling of chemicals training, and competency in operating spray equipment.
Don't neglect to supervise
When your workforce is competent, from their experience or from the instruction and training provided, you still have to provide some kind of supervision.
If they’re new, you might observe them more closely in the first few days or weeks. If it’s someone who’s learned a new thing, again you may observe more closely until you’re comfortable they’re going well.
But in general, supervision can be done through having a chat. You should speak with the worker and ask how they’re going, what’s been difficult or challenging and what’s gone well. And of course, you’ll be able to see if things are going well as you know your operations better than anyone.
If you pick up on something not quite right, have a conversation and check in to see if the worker is feeling confident about their work. If not, instruct and train as per above and you’ll see things start to improve.
Investing in your people is investing in your business – the right learning at the right time will have endless benefit for your business as well as the individual.
Safer workers are more productive and efficient, so you’ll get more done.
It also helps you meet your duty of care for work health and safety.
In the unfortunate event of a serious incident, records of training would be part of your defence against notices or prosecution.
Image and training provided by Regional Skills Training.
Topics: Safety Management System
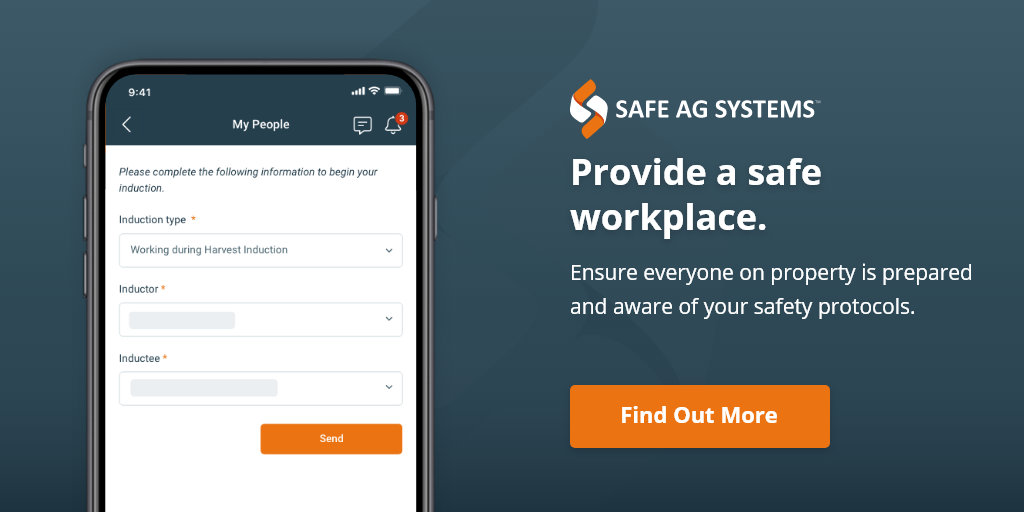
Disclaimer: Content on this website may be of relevance to users outside of Australia, but content links and examples are specific to Australia. Please check with your local authority for your country and industry requirements.